Legal for Trade Certification
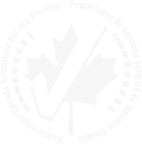
HT Scale Services is authorized by Measurement Canada to perform scale inspections pursuant to the Weights and Measures Act
In Canada, ensuring the accuracy of your weighing devices is not just good business practice—it’s a legal obligation. Scales and other measuring devices used in trade, such as buying or selling products based on weight, must be certified as ‘Legal for Trade’ under the Weights and Measures Act
This certification is crucial to ensure that your scales are operating correctly, providing accurate measurements, and maintaining consumer and business trust in all financial transactions. While Measurement Canada is responsible for monitoring the marketplace for compliance, it does not typically perform the actual inspections or certifications for legal-for-trade devices. Instead, this responsibility is delegated to Authorized Service Providers, such as HT Scale Services, which are authorized by Measurement Canada to perform scale inspections/examinations pursuant to the Weights and Measures Act
Why and When Should You Have Your Scale Inspected?
Under the Weights and Measures Act, the responsibility for the accuracy of your weighing equipment rests with you, the device owner. Regular inspections help to avoid measurement errors that could lead to penalties, loss of business credibility, or disputes with customers. These inspections ensure compliance with both Measurement Canada standards and industry-specific regulations, which is essential for maintaining fairness and accuracy in trade. If your weighing device has not been inspected within the prescribed time frame, it is considered non-compliant. Missing mandatory inspections can result in warnings, financial penalties, and even legal action. Regular inspections help avoid these issues while protecting your business operations and reputation.
- Initial Inspections:Before a device is placed into service, it must undergo an initial inspection to verify that it meets Measurement Canada’s standards for accuracy. This is mandatory for any new weighing device entering trade.
- Subsequent Inspections (Re-inspections): After the initial certification, devices used in trade may have to
be re-inspected at regular intervals. The frequency of re-inspections for weighing devices varies based on
the sector in which the device is used. For example:
- Retail Food Sector: Devices must be inspected every 5 years.
- Dairy Sector: Wholesale trade scales need to be inspected every 2 years.
- Mining and Grain Sectors: Wholesale trade devices must be inspected every 1 to 2 years, depending on their specific use.
- Petroleum Sector: Propane meters must be examined annually, while other devices are inspected every 2 years.
There are two key types of inspections:
For complete list of trade sectors and prescribed re-inspection intervals feel free to talk to one of our experts today or consult the Measurement Canada resources directly. Even if your scale is not in one of the sectors requiring mandatory re-inspection, it’s still highly recommended to have your device checked regularly to maintain accuracy, avoid costly errors, and extend the lifespan of your equipment.
Why Choose HT Scale Services?
At HT Scale Services, we are proud to be a Measurement Canada Authorized Service Provider, authorized to perform both initial and subsequent inspections to ensure your scales are Legal for Trade. We specialize in inspecting and certifying weighing devices across a wide range of industries, and we operate within Saskatchewan, with the capability to travel to neighbouring jurisdictions when needed.
By partnering with HT Scale Services, you’ll ensure that your equipment remains compliant with the Weights and Measures Act, avoiding the risk of regulatory penalties. Missing a mandatory inspection can result in financial penalties of up to $2,000, with court-imposed fines reaching as high as $50,000 for repeat offenses.
Avoid These Risks—Schedule Your Inspection Today
If your weighing device is due for inspection, or if you’re unsure of its compliance status, reach out to HT Scale Services. We’ll ensure your equipment meets all legal requirements and functions accurately, helping you avoid penalties and maintain the trust of your customers. Contact us today to schedule an inspection or learn more about our comprehensive weighing equipment services.
Calibration services
On-Site Calibration
Our Mobile Certification & Calibration Unit provides a comprehensive list of On-site Services: certification, calibration and repair of commercial weighting equipment.
Off-Site Calibration
For weighting systems that require a controlled lab environment, we also offer pick-up and delivery services to our surrounding areas.
Estimate how much scale inaccuracy can cost your business. Check our Scale Inaccuracy Calculator
Regular calibration of weighing equipment is an essential practice that ensures accuracy, reliability, and compliance,
while offering significant benefits such as enhanced customer satisfaction, cost savings, and prolonged equipment lifespan.
Customer satisfaction
Regular calibration of weighing equipment plays a crucial role in maintaining and enhancing customer satisfaction. When your scales provide precise and reliable measurements, customers can trust the accuracy of the products or services they receive, fostering confidence in your business. Consistent and accurate weighing reduces the chances of disputes over incorrect weights, ensuring that customers receive exactly what they are paying for. This builds a strong foundation of trust and loyalty. Moreover, avoiding errors related to over- or under-weighing ensures smoother transactions and operations, minimizing delays and complaints. By proactively ensuring accuracy through regular calibration, you demonstrate a commitment to quality and customer satisfaction, leading to stronger business relationships and repeat business.
Cost savings
As your scales’ components wear down over time, this can lead to inaccurate measurements. Regular calibration helps ensure that your scales stay accurate and consistent, providing you with reliable and trustworthy measurements, minimizing the risk of errors and ultimately saving you money over time. If you’re in a business that relies on weighing, such as a retail store, restaurant, or medical facility, inaccurate measurements can lead to customer dissatisfaction. Regular calibration ensures that you provide accurate and consistent measurements to your customers, maintaining their trust and loyalty.
Extending the lifespan of the scale
Consistent calibration is essential for extending the lifespan of your weighing equipment, as it helps identify and resolve potential issues early, reducing the risk of unexpected breakdowns and costly repairs. This proactive maintenance approach not only minimizes the need for frequent replacements but also enhances operational efficiency by preventing service interruptions. In the long run, regular calibration ensures that your equipment continues to function reliably, resulting in reduced long-term maintenance costs and significant cost savings, all while optimizing the performance and durability of your scales.
Compliance with regulatory requirements
In Canada, the performance of legal-for-trade scales is regulated by Measurement Canada, an agency under Innovation, Science, and Economic Development Canada. Measurement Canada is responsible for ensuring the accuracy of measuring devices, including scales used in trade, through certification, inspection, and enforcement of standards. The mandatory re-certification intervals for scales —also referred to as “re-verification” intervals—are established by Measurement Canada and vary depending on the type of device and its intended use. In most cases, re-certification is required if a scale has been repaired, relocated, or if there is reason to believe it may no longer be accurate. Furthermore, different industries have specific regulations and standards that demand precise weighing, and failure to comply can lead to penalties or fines.
Even if your scale is not operating in a trade sector with mandatory re-verification or recertification intervals, Measurement Canada still recommends regular checks and calibration to ensure ongoing accuracy . Regular calibration offers a number of significant benefits, including cost savings, maintaining customer satisfaction, and extending the lifespan of your weighing equipment. By ensuring your scales meet both Measurement Canada and industry-specific standards, you can avoid the potential consequences of non-compliance, while simultaneously improving operational efficiency and ensuring precise measurements across the board.
If you’d like to discuss the calibration of your weighing equipment or explore the possibility of setting up a comprehensive maintenance plan, please feel free to reach out to one of our experts. We’d be happy to assist you in ensuring your equipment remains compliant and in optimal working condition.
Preventative Maintenance
At HT Scale Services, we go beyond simply maintaining scales; we empower your business with the tools and insights you need to optimize your operations and make informed decisions. Preventative maintenance is a critical part of ensuring the long-term reliability and accuracy of your weighing equipment, from precision laboratory balances to heavy-capacity industrial truck and rail scales. We understand that weighing systems, especially truck scales, are the muscle of your operation. When properly maintained, they provide reliable and accurate measurements, helping you avoid costly downtime, inaccurate readings, and equipment failures. Without proper care, dirt, debris, and wear can affect the integrity of your equipment, leading to breakdowns and disruptions. With our tailored preventative maintenance agreements, we help you reduce the risk of equipment failure and costly repairs, keeping your operations running smoothly.
Comprehensive Maintenance for All Types of Weighing Equipment
Our expertise extends across all types of weighing equipment—from delicate precision laboratory balances to industrial truck and rail scales. Regular preventative maintenance helps ensure that your scales remain in top condition, reducing the risk of over- or under-weighing, which can result in financial loss, regulatory noncompliance, and diminished customer satisfaction.
Truck Scale Preventative Maintenance
Truck scales, in particular, benefit from a robust preventative maintenance program. These scales face heavy usage
and environmental exposure, making them prone to damage if not properly cared for. Routine tasks, such as daily
inspections to remove debris and checking load cell assemblies for any signs of malfunction, help reduce wear and
tear. Additionally, checking for structural damage and water build-up in pit-mounted installations ensures the
longevity and accuracy of the scale.
At HT Scale Services, we are more than happy to instruct scale operators on performing essential daily checks
and weekly maintenance to ensure their truck scale remains reliable. Beyond these tasks, we are also glad to discuss monthly, quarterly, and bi-annual preventative maintenance needs, offering tailored service
agreements to meet your specific requirements.
Comprehensive Scale Cleaning
Debris and moisture under and around your truck scale can lead to problems with your scale, leading to downtime.
Our experts are available to perform Truck Scale Cleaning to save you time, keep cost down and avoid additional
work on your weighting equipment that your business rely on.
We offer thorough cleaning services for all components of your truck scale system. From the weighbridge and load
cells to the junction boxes and display units, we ensure that every part is meticulously cleaned, removing debris,
dirt, and other contaminants that can affect weighing accuracy.
Preventative Maintenance for Precision
For more sensitive weighing instruments, such as laboratory balances, maintaining accuracy through preventative care is equally important. Even small deviations in readings can lead to significant consequences in industries like pharmaceuticals, food production, and scientific research. Our specialized maintenance plans ensure that these precision instruments stay calibrated and ready for use, protecting your business from potential losses due to inaccurate measurements.
Planned Maintenance Agreements
In addition to providing preventative care, HT Scale Services stands out by offering planned maintenance agreements that cover repairs, breakdowns, and part replacements. Our agreements are comprehensive and customizable, allowing you to choose the level of support you need based on your operational demands. Our team of experts will work with you to set up a plan that meets your specific needs.
Your Trusted Partner in Precision & Efficiency
With HT Scale Services, you are not just investing in scale maintenance—you are investing in the overall
efficiency of your business. Our preventive maintenance services, combined with our innovative software
solutions, ensure seamless data integration and analytics, empowering you to make better decisions while reducing
downtime. Whether you operate a small goods store or an industrial truck scale, HT Scale Services will customize
the best Preventative Maintenance Agreement that aligns with your budget and schedule, giving you peace of mind.
Let us be your trusted partner in precision and efficiency. We are a Measurement Canada Authorized Service
Provider and operate within Saskatchewan, Canada, and beyond, traveling to neighboring jurisdictions as
necessary. We’re ready to help you keep your scales compliant and accurate.
Scale Repair
At HT Scale Services, we understand that keeping your weighing systems operational is essential to the efficiency and accuracy of your business. We offer comprehensive repair services for a wide range of weighing instruments, from small laboratory balances to heavy-duty industrial truck and rail scales. No matter the issue, our Measurement Canada recognized technicians are ready to diagnose and repair your equipment, minimizing downtime and helping you get back to business as quickly as possible.
Repair Services for Truck and Rail Scales
Truck and rail scales are essential in industries like agriculture, mining, transportation, and construction. When
these heavy-duty scales malfunction or provide inaccurate readings, it can cause significant disruptions and
financial losses. Common issues with truck and rail scales include:
- Load Cell Replacement: Over time, load cells can wear down, causing inaccurate measurements or even complete system failure. We specialize in diagnosing faulty load cells and offering precise, reliable replacements to restore your scale’s accuracy.
- Structural Repairs: The platform of your truck or rail scale may experience damage from heavy use, exposure to the elements, or accidents. We provide structural repairs, including platform realignment and welding, to ensure that your scale continues to function as expected.
- Electronic and Digital Repairs: From faulty indicators to damaged wiring, our team can troubleshoot and repair electrical components in both analog and digital truck and rail scales. This includes replacing malfunctioning displays, recalibrating digital systems, and ensuring that your electronics are in sync with your scale’s hardware
Repair Services for Precision Laboratory Balances
Laboratory balances, often used in pharmaceutical, research, and manufacturing environments, require the highest
levels of accuracy. Even small malfunctions can lead to substantial issues, including inaccurate measurements and
disrupted workflows. Our repair services for precision balances include:
- Recalibration and Adjustment: Small inaccuracies in your lab balance can be corrected through expert recalibration. We ensure that your balance meets industry standards and provides precise measurements consistently.
- Load Cell Replacement: Just like larger scales, laboratory balances rely on sensitive load cells that can wear out over time. Our team can replace and recalibrate these cells, restoring your balance’s precision.
- Component Repairs: Whether your lab balance’s display is malfunctioning or the weighing pan is damaged, we provide component repairs to keep your system in top condition.
Repairs for Bench and Floor Scales
Bench and floor scales are commonly used in retail, manufacturing, and food industries, where accuracy is critical
for weighing goods, materials, or ingredients. Our repair services for these scales cover:
- Scale Platform Repairs: Frequent use of bench and floor scales can lead to wear and tear on the platform. We repair or replace damaged platforms to ensure your scale operates smoothly and safely.
- Indicator and Display Repairs: If your bench or floor scale’s digital display is malfunctioning or the indicator is not reading correctly, our team will troubleshoot and repair the electronics, ensuring accurate results.
- Recalibration: Over time, bench and floor scales can lose their accuracy. We recalibrate these scales according to industry standards, ensuring they provide reliable readings.
Repairs for Specialized Weighing Systems
From crane scales to hopper scales and everything in between, we offer specialized repair services for custom weighing systems used in various industries:
- Crane Scale Repairs: Used for overhead lifting and weighing, crane scales are prone to damage from heavy loads or impacts. We repair load cells, recalibrate the scale, and fix display malfunctions to keep your crane scales operational.
- Hopper Scale Repairs: Hopper scales are often used in agriculture and industrial settings to weigh bulk materials. Common issues include load cell misalignments, faulty sensors, and mechanical wear. We offer full-service repairs, ensuring that your hopper scales deliver accurate results without interruptions.
Why Choose HT Scale Services for Your Repairs?
Our highly trained technicians have extensive experience in both hardware and software repairs, ensuring a holistic approach to your weighing system’s needs. We are proud to be a Measurement Canada Authorized Service Provider, meaning that not only can we repair your scale, but we can also ensure it meets all regulatory requirements after repairs are completed.
Whether your scale requires a simple calibration or a more extensive structural repair, HT Scale Services has the expertise and tools to get the job done right. From regular maintenance to emergency repairs, we are your trusted partner in precision & efficiency.
System Integration & Data Analytics
HT Scale Services goes beyond hardware repairs by also offering advanced software solutions and system diagnostics for integrated weighing systems. In today’s data-driven world, scales are often connected to broader enterprise systems, including inventory management, and data collection platforms.
- Software Integration and Repair: If your weighing system interfaces with software for data collection, reporting, or analysis, our team has the expertise to identify and fix integration issues. Whether you need updates to your existing software or troubleshooting for a malfunctioning interface, we ensure seamless communication between your scales and software systems.
- Data Analytics and Automation: We can help repair and optimize any malfunctioning data systems associated with your weighing equipment. For businesses that rely on real-time weighing data to inform decisions, we ensure that your equipment integrates smoothly with your data analytics platforms, delivering reliable results.
- Remote Diagnostics and Repairs: If your system allows for remote diagnostics, we can troubleshoot and repair certain software issues without needing to be on-site, saving you valuable time. For integrated weighing systems, this service can drastically reduce downtime, giving you the confidence that your system will be up and running in no time.
After Sale Support
Our commitment to you doesn’t end after the sale or repair. We pride ourselves on providing industry-leading After Sale Support that ensures your weighing systems continue to perform optimally for the long term. Whether you’ve purchased new equipment, had an existing system repaired, or need ongoing guidance, we’re here to offer the comprehensive support you need to keep your operations running smoothly and efficiently.
Ongoing Customer Support
Your business needs reliable and accurate weighing systems to maintain operational efficiency and profitability.
That’s why we offer ongoing customer support to assist with any challenges or questions you might encounter
after installation or repair. Our dedicated support team is always ready to provide expert advice on:
- System Troubleshooting: Encountering unexpected issues? Our technicians are available to guide you through troubleshooting procedures and provide step-by-step solutions, ensuring minimal disruption to your operations.
- Technical Assistance: Whether you need help navigating new features on your equipment, understanding software integrations, or resolving calibration issues, our team is here to provide technical support every step of the way.
- Maintenance Guidance: Proper maintenance is key to extending the lifespan of your weighing equipment. We offer ongoing advice and recommendations on best practices for daily and periodic maintenance. Our team can instruct operators on proper daily checks and provide guidance on maintaining the accuracy and functionality of your scales.
Post-Repair Validation
After any repair or service, it’s crucial to ensure that your weighing system is back to performing at the highest
standard. At HT Scale Services, we go the extra mile with our post-repair validation process. This ensures that
your equipment is not only fixed but also restored to meet all regulatory and performance standards.
- Recalibration and Testing: Once repairs are completed, we thoroughly recalibrate and test your weighing system to confirm it is functioning accurately. Whether you’re dealing with a laboratory balance or an industrial truck scale, we ensure the system meets Measurement Canada standards and your unique operational requirements.
- Compliance Assurance: As a Measurement Canada Authorized Service Provider, we ensure that your weighing equipment complies with the Weights and Measures Act after repairs, so you can operate with complete peace of mind. We perform final tests and issue the necessary certification where applicable, so you know your equipment is legally approved for trade.
- Data Verification: If your weighing systems are integrated with software or data analytics tools, we validate the accuracy of your data collection after repairs. We make sure that your equipment is communicating seamlessly with your software platforms, giving you consistent and reliable data for informed decision-making.
Training & Education
Part of our After Sale Support includes providing education and training to your team. Whether it’s a new weighing
system installation or a repair on existing equipment, we offer training sessions tailored to your operators and
maintenance personnel. This helps ensure that everyone using the equipment understands its functionality and can
perform essential checks to maintain its accuracy.
Our training services include:
- Operator Training: Comprehensive instructions on how to use your weighing systems effectively, avoid common issues, and identify signs of malfunction before they become costly repairs.
- Maintenance Education: Training on how to carry out essential routine maintenance tasks, which helps reduce the likelihood of damage, prolongs equipment lifespan, and ensures accuracy.
Extended Service Plans
To give you even more peace of mind, HT Scale Services offers customizable Extended Service Plans that go beyond the typical warranty. These plans provide you with
access to priority support, scheduled maintenance, and discounted rates on repairs, ensuring your equipment stays
operational year-round.
With our After Sale Support, you can count on us to be a partner in the continued success of your business. From
post-repair validation to ongoing guidance and training, HT Scale Services is committed to supporting your needs
long after the sale is complete.
Why Choose HT Scale Services for After Sale Support?
- Trusted Expertise: We understand the intricacies of weighing systems and are always prepared to offer reliable solutions.
- Tailored Support: Whether you operate a small-scale retail business or an industrial operation, our support services are tailored to meet your unique needs.
- Comprehensive Approach: From hardware to software, our holistic approach to After Sale Support ensures that every aspect of your weighing system functions in harmony for optimal performance
- Proactive Solutions: We don’t just fix problems — we work with you to prevent them, ensuring that your equipment is well-maintained and operating at its best.
24/7 On-Call Support
At HT Scale Services, we understand that equipment malfunctions don’t always happen during regular business
hours. When your weighing system breaks down unexpectedly, it can create costly delays, impact your bottom line,
and disrupt your entire operation. That’s why we offer 24/7 Emergency Repair Services as a part of our
extended Maintenance Agreements—because
we know that in critical industries, every minute of downtime matters.
Our emergency repair team is available around the clock, ensuring that no matter when your issue arises, we’re
just a phone call away. Whether it’s a truck scale breakdown in the middle of the night or a malfunctioning
precision balance that halts your lab operations, we prioritize urgent repairs to restore functionality as quickly as
possible.
- Fast Response Times: We know that time is money, especially when your operations are on hold. Our 24/7 on-call technicians are trained to diagnose and repair issues swiftly and efficiently, minimizing your downtime and keeping your business running smoothly.
- Comprehensive Solutions: From electrical malfunctions to damaged load cells, our emergency repair services cover every aspect of your weighing system. No matter the issue, we come prepared with the tools and expertise to diagnose and repair the problem on the spot.
- Support Across All Sectors: Whether it’s a retail scale in a busy store or a high-capacity industrial scale at a truck weigh station, our emergency repair services cater to all sectors. We have experience working with a variety of scales, so you can trust us to resolve your issue, regardless of the equipment type.
By offering 24/7 emergency repair services, HT Scale Services ensures that your weighing systems remain operational, no matter when a problem arises. Rest easy knowing that our expert technicians are available around the clock to support your needs.